Design Next-Generation Data Center Cooling Systems with Silicon Carbide
Article
Data centers form the backbone of the digital world, housing the massive servers that power the internet, cloud computing, and other data-driven services. As the demand for these services grows, so does the amount of energy they consume.
In the United States, data centers consumed an estimated 90 Terawatt-hours (TWh) of electricity in 2020, representing about 1.8% of total U.S. electricity consumption. This is expected to grow to 140 Twh by 2030, an increase of 56%. A global increase in Artificial Intelligence (AI) applications is placing a further strain on data center power consumption, necessitating additional servers and, in turn, more power to run them. The global growth in data centers makes it imperative that system designers find new and novel ways to reduce power consumption, while improving computing capacity.
Data centers are complicated systems and there are many ways to reduce overall power consumption. Among the various subsystems, data center cooling systems account for a significant portion of its total energy consumption, with estimates ranging from 20% to 45%. The exact percentage can vary based on the type of cooling system used, the climate of the location, and the IT equipment being cooled. The efficiency of cooling systems within data centers can be dramatically improved with silicon carbide leading to up to 50% reduction in system losses, achieving global efficiency standards, and enhancing system performance with reduced audible noise, faster rotation speeds and more precise control.
Up to 60% lower losses system-wide with 1200 V SiC MOSFETs
Data center cooling systems consist of an AC-DC (Active Front End) stage followed by a DC-AC inverter stage. By using six 1200 V SiC MOSFETs (C3M0075120K) in place of IGBTs in the AFE of a three-phase supplied, 11 kW cooling system, designers can achieve a 0.9% efficiency improvement. Additional improvement can be achieved when the inverter is also upgraded with drop-in 1200 V C3M0075120K SiC MOSFET.
Below, Fig.1 and Fig.2 show the comparison of conduction loss and switching loss of a typical 1200 V SiC MOSFET and a 1200V IGBT with same rated current. Under lower loads the SiC MOSFET conduction losses are as much as one-half that of the IGBT and offers up to 90% less switching losses than the IGBT by eliminating the turn off tail current.
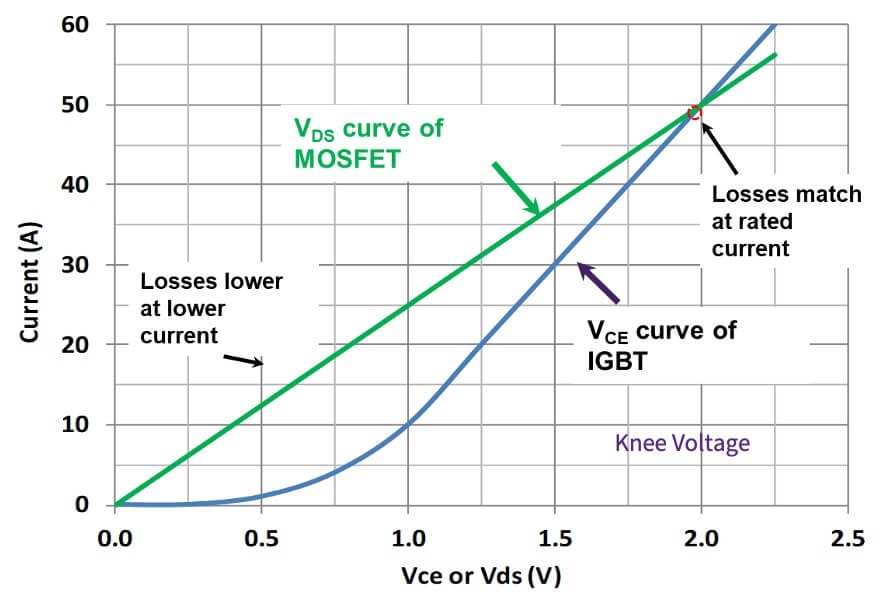
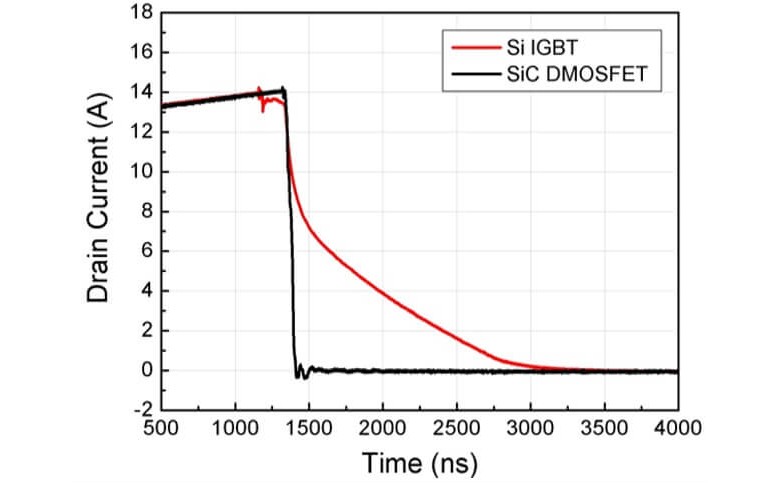
With lower switching losses, Wolfseed SiC MOSFETs can operate at much higher switching frequencies than IGBTs, allowing system designers to use smaller and lighter transformers in variable speed fan drives. Smaller transformers mean reduced copper losses, further contributing to energy efficiency improvements. Additionally, higher switching frequencies enable more precise speed control of the fan, ensuring optimal cooling performance at varying load conditions. With the improved light load conduction loss, SiC MOSFETs enable a much flatter, high efficiency curve over all load conditions, further benefiting variable speed applications.
Shown in Fig.3, Wolfspeed’s newly released 11 kW High-Efficiency Three-Phase Motor Drive Inverter (CRD-11DA12N-K) was designed to test Wolfspeed’s 1200 V SiC MOSFETS in industrial heating and cooling applications. This design accomplishes peak efficiencies of 99% and a full load efficiency of 98.6%; wide operating voltage range of 550-850 VDC and closed loop sensorless field oriented control. The test results are shown in Fig.4 and Fig.5.
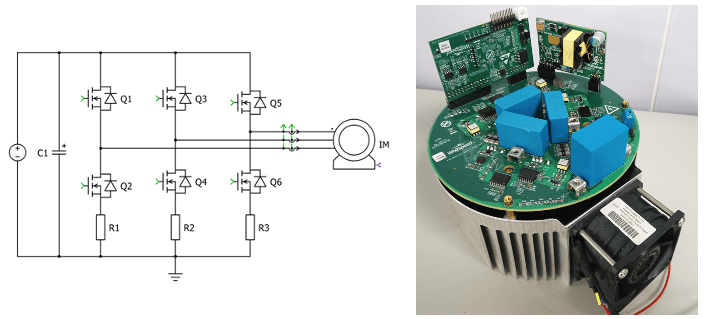
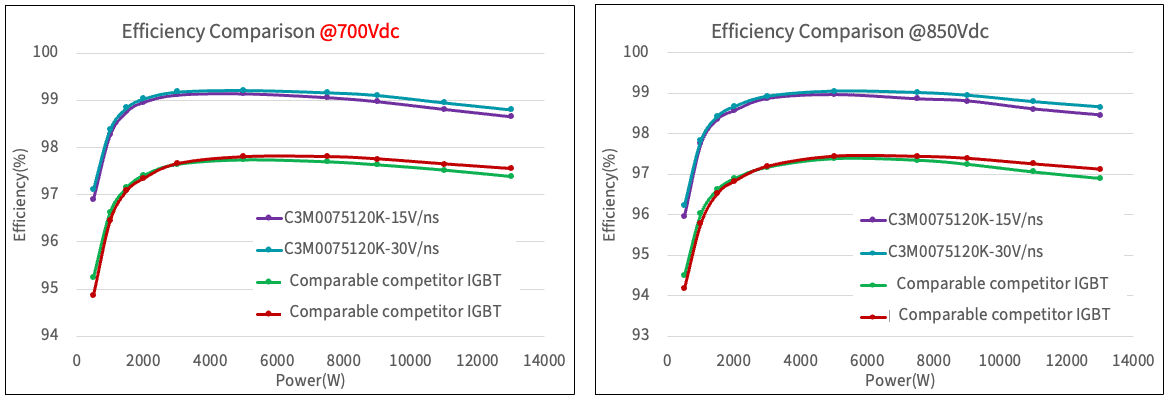
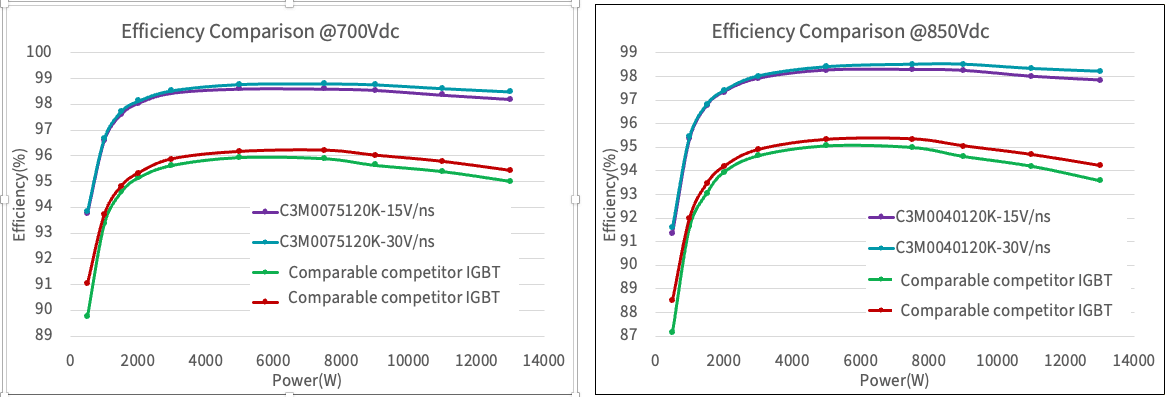
As shown above, by replacing silicon IGBTs with silicon carbide, running at 16kHz, motor drive efficiency can be improved by >1.2%, a >50% reduction in power losses. As IGBT device efficiency drops under high operating frequency, silicon carbide devices can easily double the operating frequency from 16 kHz to 32 kHz to help shrink the sizes of passive components, while maintaining >98% efficiency.
Achieve higher efficiency with smaller heat sinks with SiC
Silicon carbides presents a tremendous value at the system level in data center cooling systems, delivering high efficiency and power density with improved thermal resistance, and enabling overall smaller, less expensive cooling systems. For example, in a 25kW compressor with a six-switch 2-level active front end (AFE) switching at 45 kHz, designers can realize a 1.3% efficiency improvement with SiC in the front-end stage when benchmarking against a silicon switching at 20kHz when discrete IGBTs are replaced with Wolfspeed’s C3M0032120K discrete MOSFETs (1200V / 32mOhm). A 1.1% efficiency improvement can be achieved in the inverter when Wolfspeed’s 30 A rated full-bridge power module CCB032M12FM3 (Wolfpack) is conservatively benchmarked against a 50A and 100 A rated Si-IGBT module, both switching at 8 kHz. Together, these two changes yield an impressive 2.4% in efficiency improvement, 50% reduction in losses system wide.
One of the most noteworthy improvements that can be made in the inverter with silicon carbide is a significant reduction in system-generated heat, enabling designers to use smaller heat sinks and design overall smaller, lighter compressors for data center cooling systems, or enable more cooling using a similarly dimensioned compressor as before.
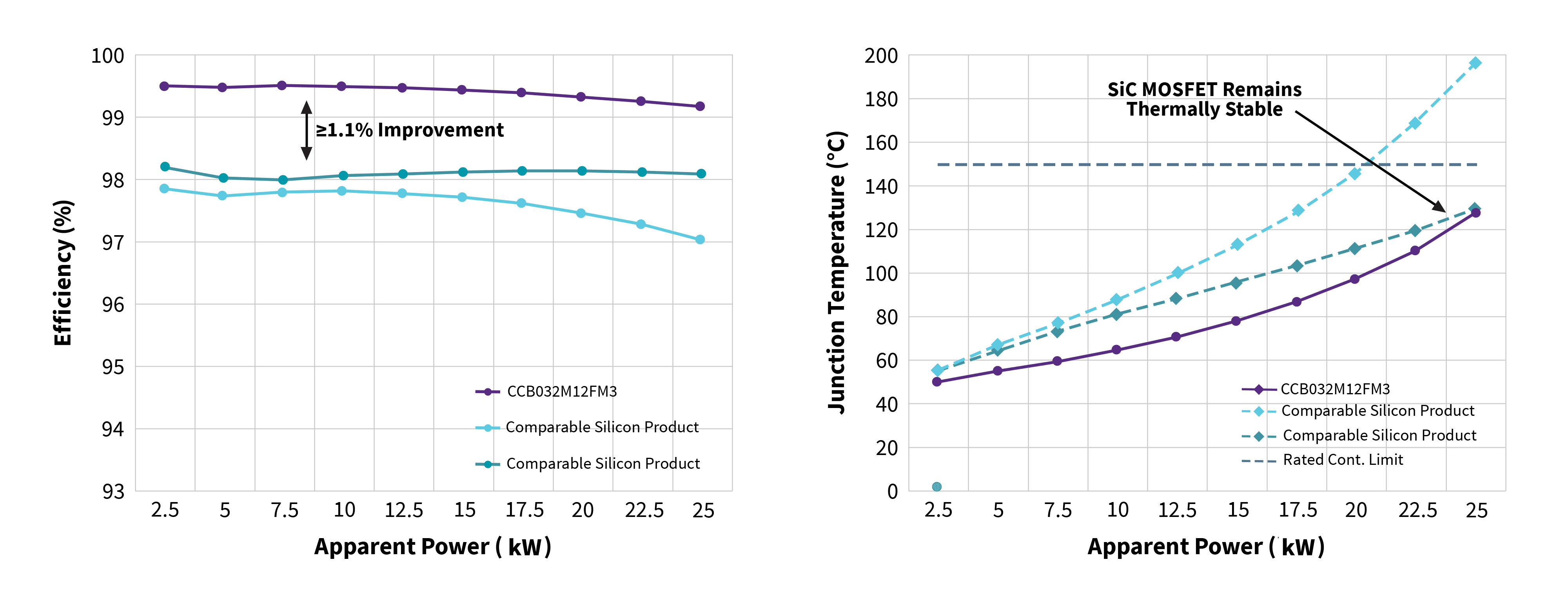
Results in the graphs above have been achieved with a 77% smaller heat sink for the silicon carbide inverter as compared to IGBT. Despite a much bigger heat-sink for Si modules, the 50 A IGBT module’s junction temperature is still significantly above the 150°C temperature limit, but the 32 A SiC module and the 100 A IGBT module end up at the same junction temperature of around 129°C. Also noteworthy is that efficiency in the silicon carbide inverter increases by 1.1%. Additionally, the efficiency improvement above is not only at peak loads but also at partial loads. At some partial loads the efficiency improvement is higher which is ideally suited to the typical load profiles of data center cooling systems.
In summary, using a reduced and more optimized-heat sink with silicon carbide in a 3-phase supplied, 25 kW system results in an overall 2.4% efficiency improvement with a 600 W reduction in losses while enabling smaller, lighter overall cooling systems.
In Conclusion
In conclusion, replacing traditional silicon carbide IGBTs with Wolfspeed silicon carbide 1200 V MOSFETS and power modules in 11 kW and 25 kW data center cooling systems can dramatically improve overall system efficiency, delivering up to 2.4% increases in overall system efficiency. High efficiency improvement at higher power levels is possible throughout the load profile, resulting in massive energy savings. Silicon carbide also offers improved power density due to smaller passive components and heat sinks and leads to overall system cost and size optimization. Additionally, high junction temperature possibilities and improved thermal dissipation of SiC devices together with lower losses allow designers to build more compact systems, enabling an easy integration of drives and motors and ushering in the next generation of efficient data center cooling systems.