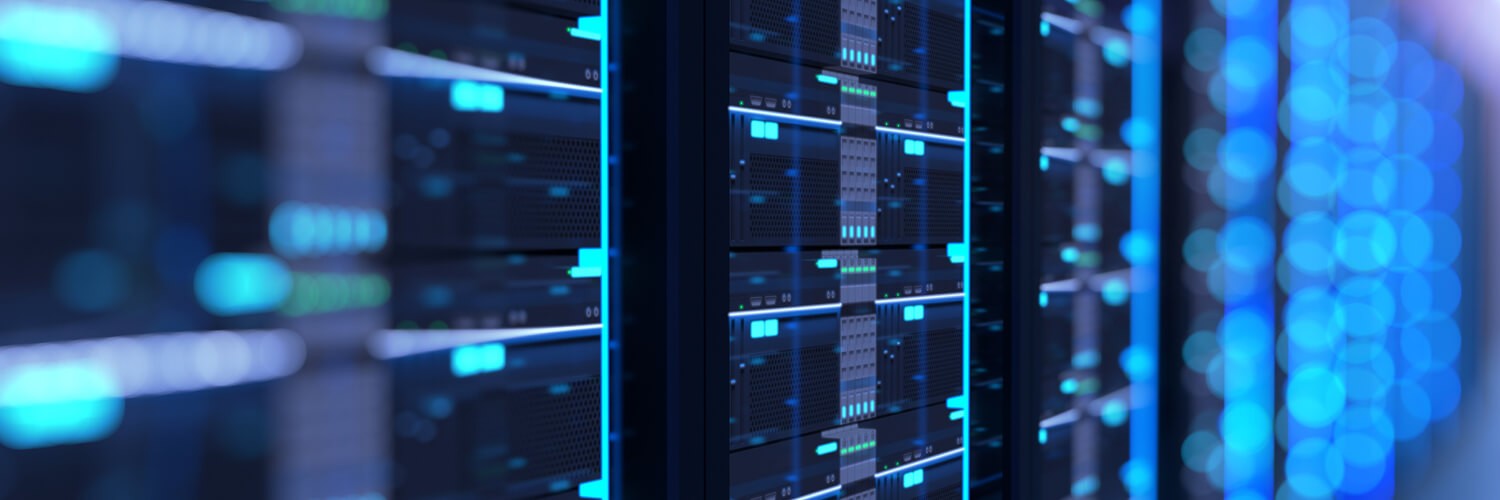
Applications
Industrial
The world runs on power, and we see a future where the world can do much more with much less.
Leading the Transformation from Si to Silicon Carbide
We believe the unique attributes of Silicon Carbide provide the means to radically reduce the amount of energy the world consumes. With industry-leading performance, superior thermal capability and field-proven reliability, Wolfspeed’s Silicon Carbide (SiC) semiconductors and expertise give power systems designers the products and the tools needed for success.
Industrial Applications
Knowledge Center
Practical Tools for Designing with Silicon Carbide in Industrial Motor Drives
Simplify, accelerate and de-risk the design process when designing industrial motor drives with silicon carbide and easily access IE4 and IE5 efficiency standards.