New SiC Power Modules Deliver Greater Power Densities in Smaller Packages Than Si IGBTs
Article
Introduction
With the shift toward electrical power for a wide range of applications, including power generation, energy storage, and transportation, comes the need to build higher performance electrical conversion and control systems to fuel the future of electric-powered systems. To do so, there is a greater demand for more compact, higher power density, and high temperature operating power modules.
Until recently, the power module market has been dominated by silicon insulated-gate bipolar transistors (Si IGBTs). The shift in demand and focus on better performance has made these legacy modules less desirable for high power applications, which has led to the rise of silicon carbide-based power devices. New SiC components are able to deliver higher voltage and current performance (power) in less space than their silicon-based counterparts, enabling high-power density modules with minimal parasitics and high temperature operation.
This article aims to educate power engineers and professionals on the advantages of the latest SiC devices in power modules compared to legacy Si IGBTs for modern power electronics applications. A comparison of the two technologies is outlined, as well as a demonstration of the capabilities of the latest full SiC power modules in a three-phase inverter reference design application.
Figure 1:
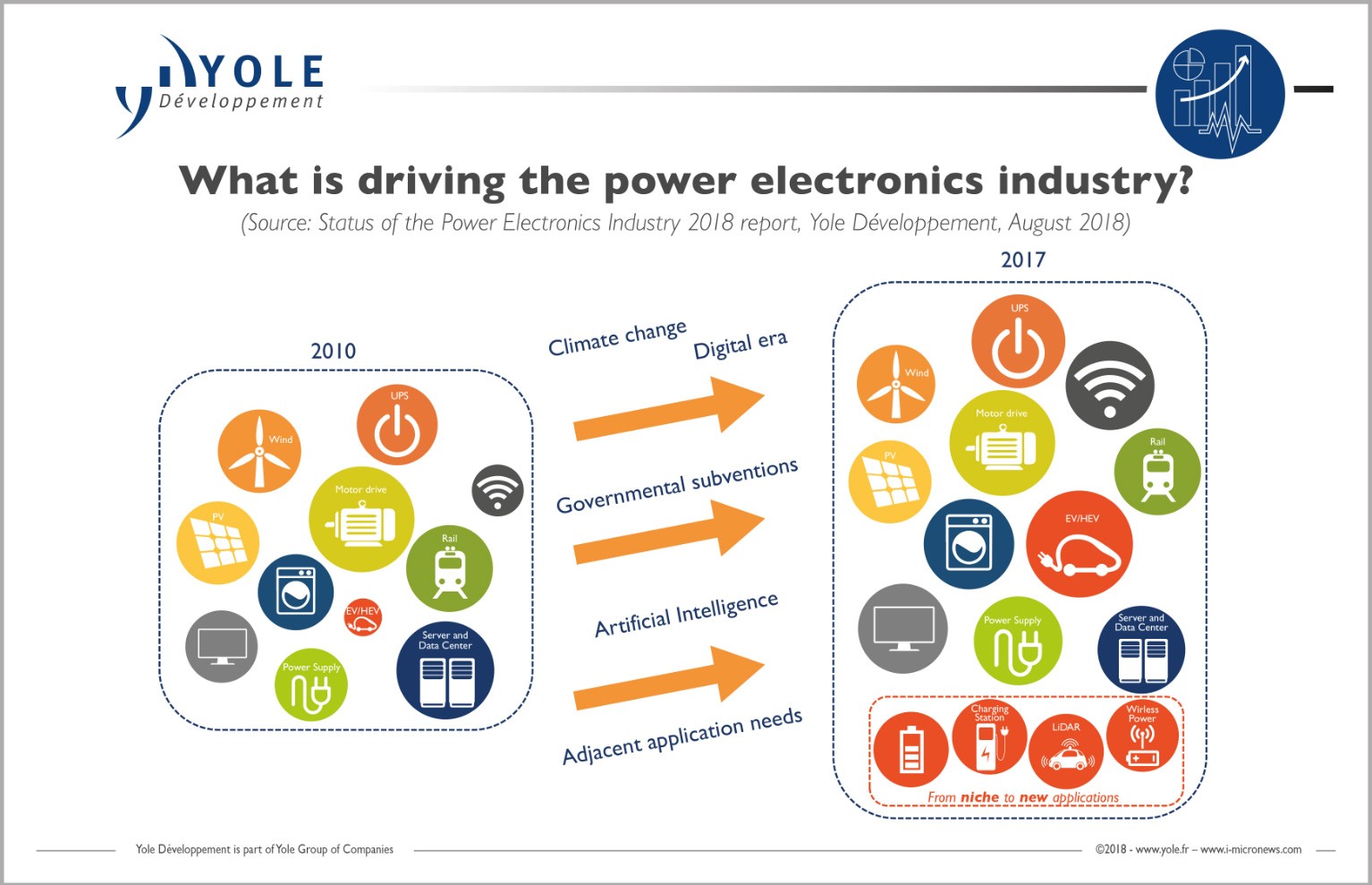
The power electronics industry is experiencing a boom of growth in both traditional transportation and power supplies, as well as emerging applications, such as electric vehicles, renewables, and data centers.
Source: Yole development 2018
Trends in power module electronics
Power modules are becoming increasingly sought after in the power electronics industry, as they are easily deployed and are often compatible with industry-standard bus connections, control/sense interconnect, and commercially available heat sinks. Using modules enables power system designers to focus on getting the greatest performance out of a power system, instead of having to spend valuable engineering hours developing custom housing, heat sinks, bus interconnects, and integrating/tuning sensing and control electronics.
More than ever, the demand to develop power systems more rapidly and efficiently is increasing as many of these applications are growing at staggering rates (see Figure 2). The demand for renewable energy systems, electric vehicles, train/rail transportation, more efficient grid systems that include energy storage, and uninterruptible power supplies (UPS) that keep data centers and critical electrical systems running seamlessly, are all applications seeing double-digit growth year over year.
Figure 2:
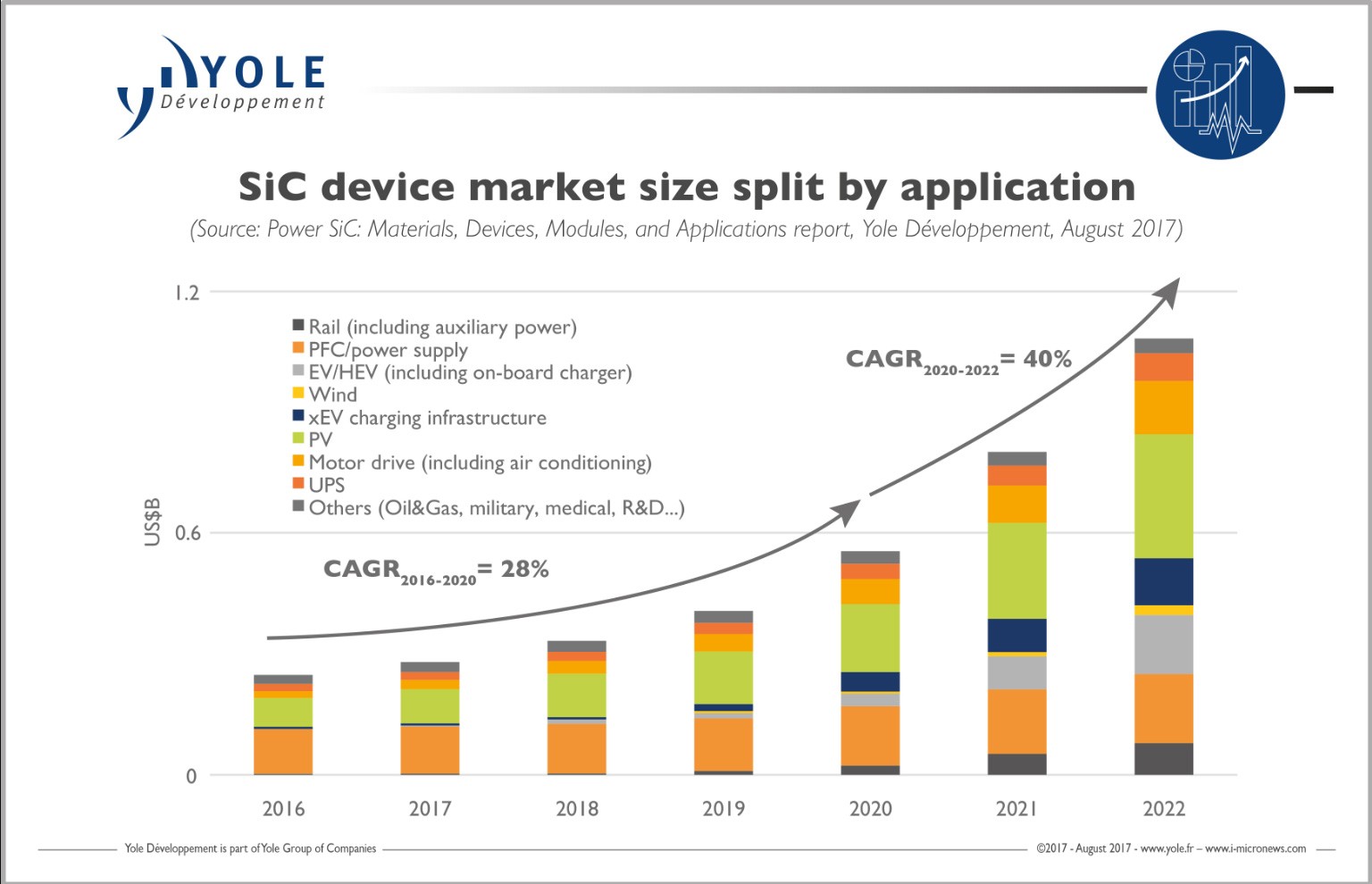
The demand for SiC devices has increased as the markets using SiC materials and power modules continue to grow. Source: Yole development 2017
How new SiC devices exceed legacy Si IGBTs
As there is a greater demand of power modules for new applications and advancements of legacy applications, there are also opportunities for innovation to enhance the performance and capabilities of power modules. Traditional power modules are comprised of Si IGBTs, which have been around for several decades. These have specific footprint and power module construction features of these Si IGBTs have driven the common expectations for power density and construction limitations.
However, with the advent of new power modules that are optimized for SiC, these standards and perceptions require adjustment. The latest SiC transistors are developed using silicon carbide semiconductors, which exhibit a bandgap voltage nearly three times that of silicon, an over 10-fold greater critical field, more than five times greater thermal conductivity, and an overall power device figure of merit that vastly exceeds silicon’s capabilities (See Table 1).
Table 1: Si and SiC Semiconductor Properties
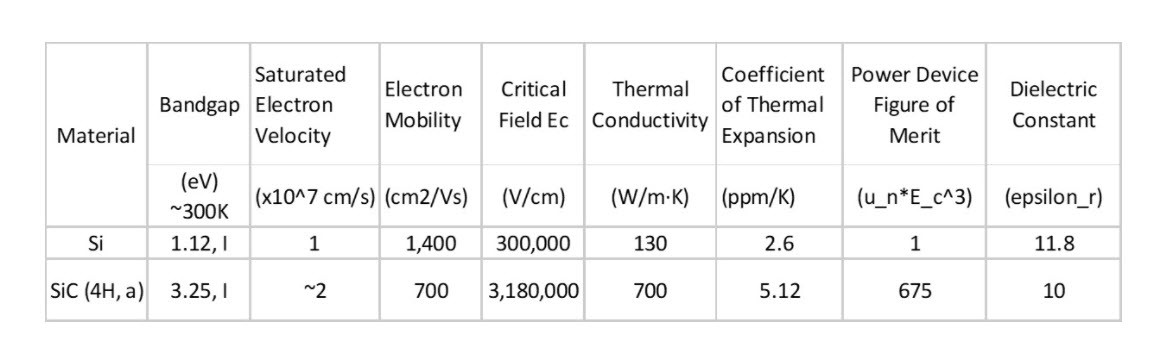
The benefits of SiC combined with the use of MOSFET type transistors as opposed to a bipolar junction transistor typology, enable new full SiC power devices to deliver much higher voltage and current operation in devices that are a fraction of the size of comparable Si IGBTs. Moreover, these SiC devices are able to provide much lower (>5×) switching losses than Si IGBTs; hence, SiC device switching speeds can be set several times beyond (10-50 kHz typical) Si IGBT’s limited switching speeds. Lower conduction losses of SiC devices also allow for greater efficiency at light loads compared to Si IGBTs.
Innovations unleash SiC power modules to commercial markets
When it comes to power modules, the power device itself is only part of the story. The design and integrated features of an assembly and affiliated electronics can also greatly impact the performance and functionality of the overall power module. As a result, careful design is needed to optimize the power devices performance and include features that minimize the loop inductance, facilitate high temperature operation, and account for the interconnect complexity of appropriate applications.
Wolfspeed has done all of this with their latest XM3 full SiC power modules, along with integrating several features that reduce the power module footprint, provide greater power density, and reduce BOM count, while improving performance. Many of the features of the new XM3 SiC module technology resemble highly sophisticated low-volume custom production systems, but the XM3 modules are made to deliver such performance and features for high-volume applications at an extremely competitive price point.
Figure 3:
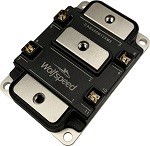
The Wolfspeed XM3 SiC power module is compact, power dense, and extremely rugged, making it ideal for a wide range of high power industrial, rail, and automotive applications.
Pinnacle of full SiC power modules
The new XM3 power module (CAB450M12XM3) is built using the latest generation of Wolfspeed’s SiC MOSFET bare die technology and is conduction-optimized. This new generation of power module features high temperature operation and low loop inductance, along with an extremely high power density footprint that exceeds that of both Si IGBT and other SiC modules. The blocking voltage of these modules can reach peak ratings of 1,200 V with current ratings to 450 A.
XM3 key features:
- 100 kW to 300 kW peak power levels with high power density (32 kW/L)
- High temperature (175°C) operation
- Low inductance (6.7 nH) design
- >5× lower switching losses results in higher switching frequencies (10-50 kHz typical)
- Delivers low conduction losses without intrinsic knee-voltage for enhanced light load efficiency
- Integrated temperature sensor on low-Side switch position (close to external NTC pin location)
- Built-in voltage sensing (De-Sat) connection for easy driver integration
- Offset middle terminal layout allows for simple & low-inductance busbar interconnection
- High reliability silicon nitride power substrate to address demanding markets with enhanced power cycling capability
Though the XM3 modules exhibit excellent electrical characteristics, they also are designed with high density integration in mind. These new SiC modules are built using an extremely compact 80 mm × 53 mm × 19 mm module package, which enables an operating power density of greater than 30 kW/L, which results in a 60% smaller package than other comparable rated power modules. This fact, combined with an optimized bus bar interconnect strategy that reduces system-level parasitic inductance, enables the realization of power module efficiencies greater than 98%.
Key reference design – 300 kW Three Phase Inverter
There are many applications that can benefit from the high-power density and low loop inductance of the XM3 SiC power modules. The following is a description of Wolfspeed’s reference design for a 300 kW threephase inverter, ideal for motor and traction drives, grid-tied distributed generation and high-efficiency converters.
Figure 4:
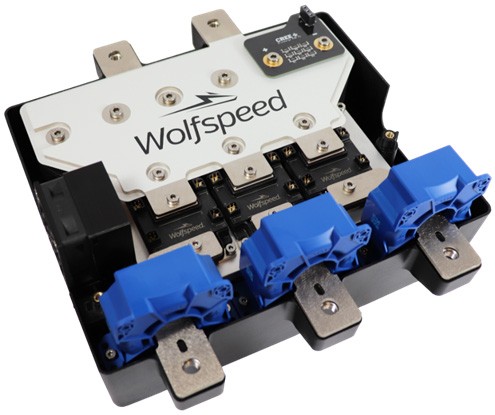
The 300 kW three-phase inverter demonstrates system-level power density and efficiency obtained by using Wolfspeed’s new XM3 module platform. The three-phase inverter has greater than 2X the power density of comparable Si based designs and greater than 98% efficiency.
Keeping with the design philosophy of the XM3 power modules, this three-phase inverter design is optimized to realize a low-inductance and high-ampacity circuit that reduces cost and complexity of the overall system. Furthermore, overlapping planar bus bar structures are used to minimize the introduction of additional inductance and the capacitors used to mitigate ripple are also low-inductance components. These factors result in minimal parasitic inductance and allow for higher switching speeds at greater efficiency levels.
Along with other design features, including a micro-deformation liquid cooled cold plate by Wolverine™, the resultant inverter measures 279 mm × 291 mm × 155 mm with a power density of 32.25 kW/L. This inverter reference design is able to provide 1.2 kV operation and reach 250 kW of power in a fraction of the volume of Wolfspeed’s previous inverter reference designs. Moreover, in practical testing, the three-phase inverter design leveraging the XM3 SiC module technology was able to demonstrate very low switching loss along with minimal ringing in spite of a very low gate resistance used during the test (See Figures 3 & 4).
Figure 5:
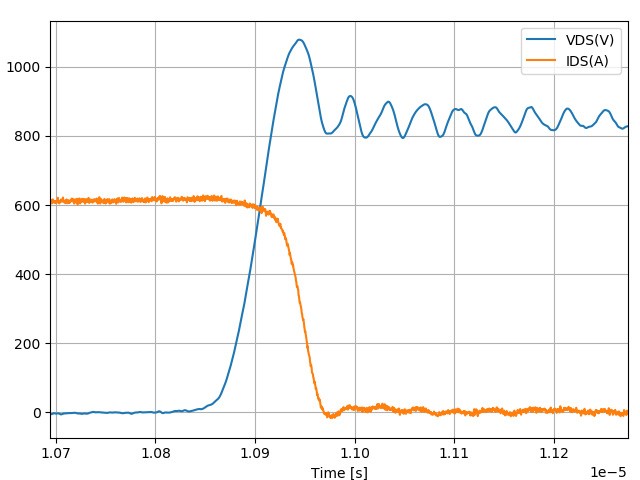
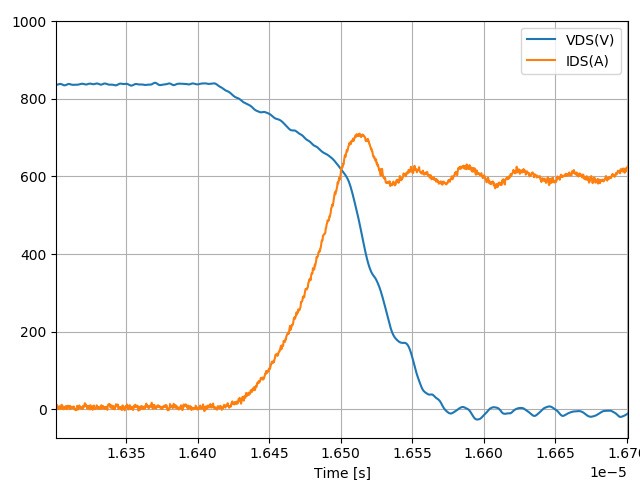
Switching waveforms for lower switch during turn-off (left) and turn-on (right).
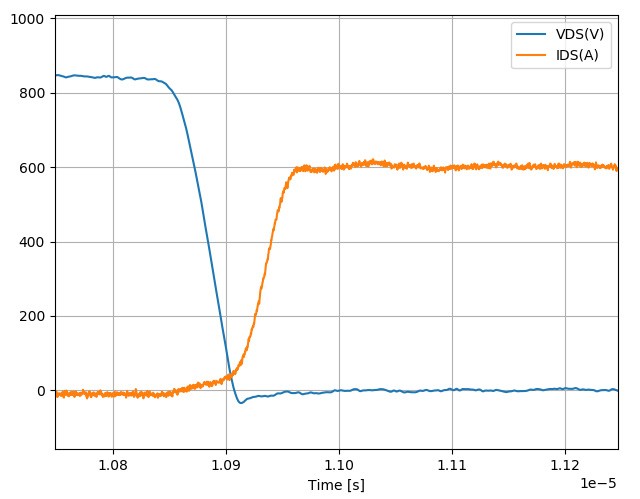
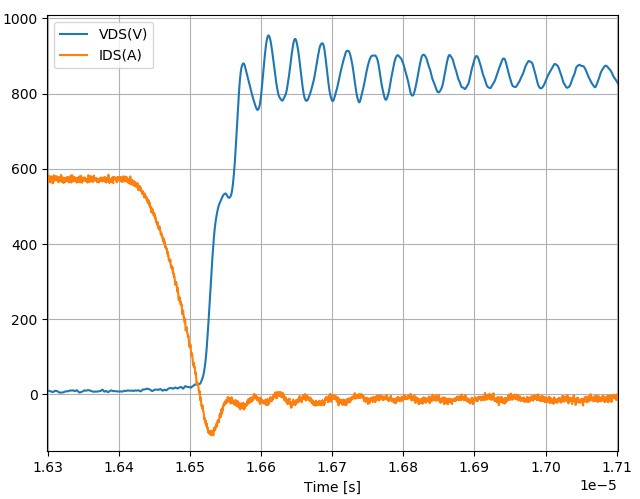
Switching waveforms for upper switch during turn-off (left) and turn-on (right).
SiC module use cases and applications
Wolfspeed’s new XM3 SiC power modules are designed to operate in an array of applications, which include modern motor and traction drive, UPS, and EV charger systems. Beyond this, any application with power levels between 100 kW and 300 kWs that experiences large magnetics and requires substantial input and/or output filters can benefit from the densification opportunity enabled by the XM3’s compact package and optimized bus bar design.
Moreover, systems that have been limited to several kilohertz switching speeds with Si IGBT modules, can benefit from a several factor increase in switching speeds with full SiC modules. This includes data center power, factory automation systems, and other circumstances where there are high system level costs, where greater efficiency and reduce module count can result in operational and system level cost savings. Furthermore, the physical ruggedness and temperature operation of SiC MOSFET die exceeds that of Si IGBT die, and these new power modules are well suited to operation in extreme environments and rugged applications, such as trailway, traction, and heavy-equipment industries that are increasingly being electrified.
Conclusion
The growth and new market forces in the power electronics industry are driving performance requirements beyond the technical limitations of silicon bipolar power modules. Hence, Wolfspeed has adapted their excellence in silicon-carbide technology to the latest and most power dense of high-volume and commercially available power modules, the XM3 53 mm full SiC power module. With a compact footprint, high-temperature operation, fast switching speed capability, and low-inductance design, these new XM3 modules enable much smaller footprint power systems with greater efficiency, just in time for emerging motor, converter, inverter, and power supply applications.