Designing with Silicon Carbide in Unidirectional On-Board Chargers
Article
EV on-board chargers (OBCs) enable EVs to be charged anywhere that AC power is available. It can take several forms based on power level and functions. Charging powers vary from less than 2 kW in applications such as electric scooters to 22 kW in high-end EVs. Traditionally, charging power is unidirectional. A new trend is to add bidirectional function into OBCs so that EVs can be a mobile energy storage system. This paper will focus on unidirectional OBCs only and discuss the advantages of silicon carbide (SiC) in higher-power applications above 2 kW.
The AC voltage and current available from the electric grid imposes a limitation on the OBC design. The standard household receptacle in the U.S. can provide up to 1.92 kW (120 VAC, 15 A), and the 208- or 240- VAC U.S. split-phase system can provide up to 19.2 kW depending on the capacity of the branch circuit breaker. The standard household voltage in the EU is 230 VAC, and three-phase utility is available.
Figure 1 shows typical uses for low-, medium-, and high-power OBCs. Low-power OBCs are popular for e-bikes and low-power EVs in India and China. Currently, the medium-power market (2~7.4 kW) is the most popular for many common battery EVs in Europe and the U.S. Medium-power OBCs use single-phase AC and charge EV batteries of about 400 V, but as demands for long range continue to increase, the market is trending toward 800 V batteries with higher-power three-phase OBCs of 11 kW and 22 kW; these offer faster charging times and lower currents for a given power level.
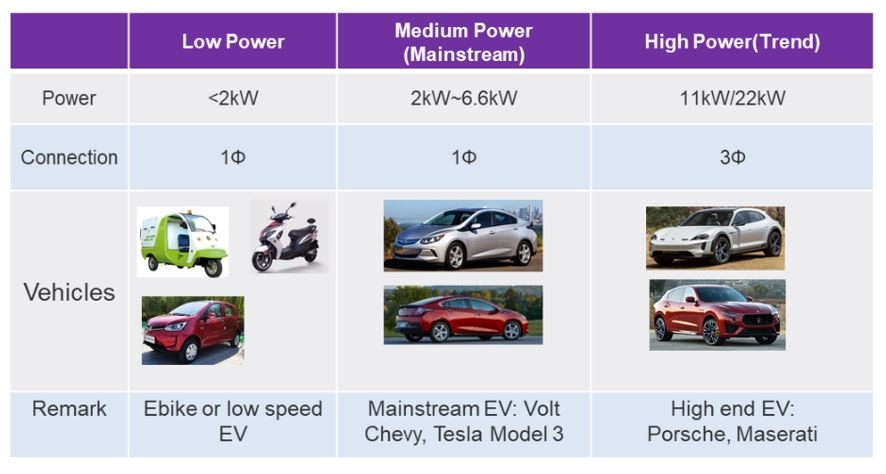
Regardless of grid power, the main building blocks in an AC-to-DC OBC are a power-factor–correction (PFC) block and a DC/DC converter. The main design tradeoffs are between power density, efficiency, and cost. This article breaks down each power level and discusses the device choices for each class. SiC MOSFETs and diodes can provide much better efficiency and power density than Si devices. The main opportunity for SiC lies in medium- and high-power (>3 kW) OBCs.
Low-power OBC architectures (<2 kW)
At the lowest end of the market, silicon (Si) MOSFETs and diodes are preferred when cost is the highest priority, although they have disadvantages compared with SiC for high-power applications. Figure 2 shows a boost PFC and a half-bridge LLC converter; this combination is popular for low-power cost-sensitive OBC applications. Normally, this architecture supplies a relatively low voltage battery (<60 V) from a single-phase 120 V/240 VAC supply and can achieve peak system efficiencies of ~93%.
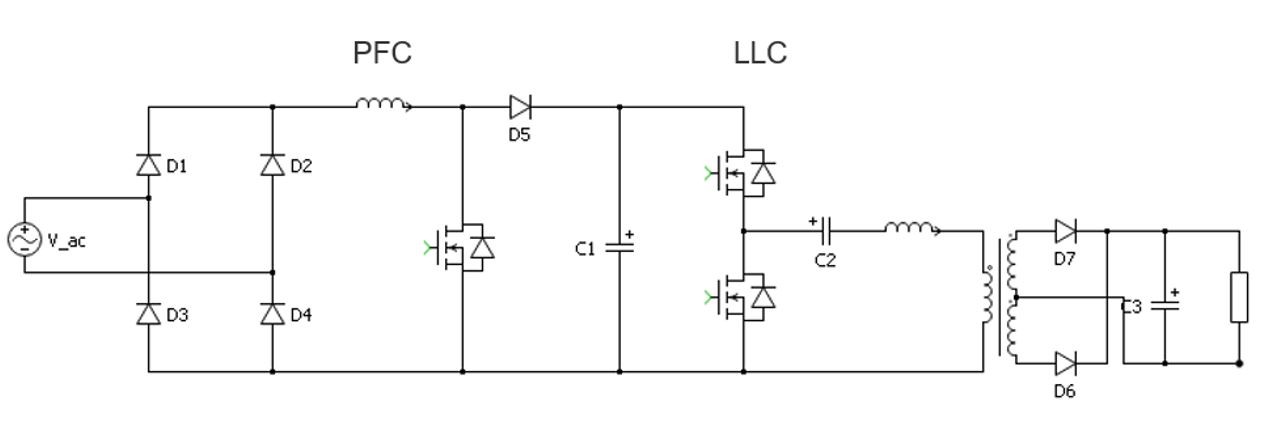
Medium-power cost-sensitive OBC architectures (3.3–7.4 kW)
For medium-power architectures, the designer can choose between cost-sensitive and high-efficiency options. The medium-power cost-sensitive design (Figure 3) uses the same PFC topology as before but replaces the half-bridge LLC DC/DC converter with a full-bridge design to support 400V battery. With a higher battery voltage, the power loss on the output rectifiers can be reduced. Hence, the efficiency is improved from that of the low-power OBC discussed above, with peak efficiency of ~94%.
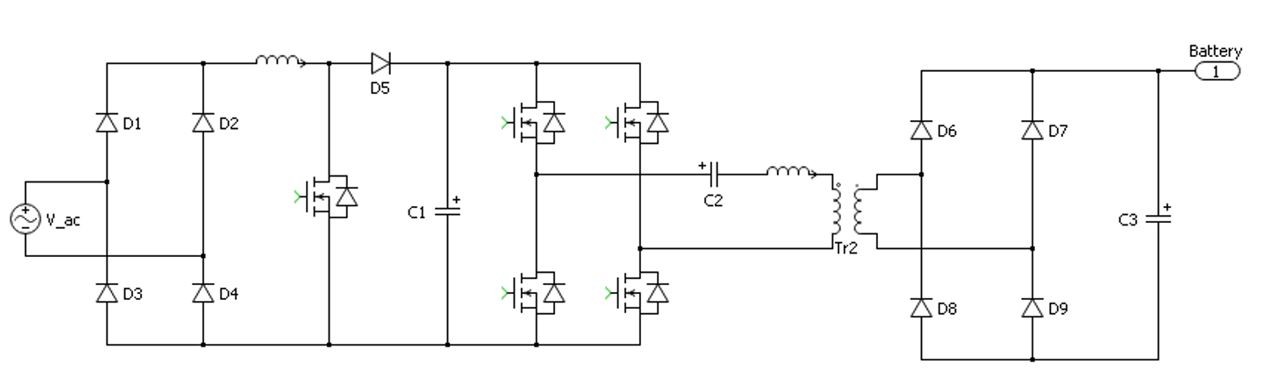
Si MOSFETs will still dominate in the active switch sockets in the low-cost design. The main opportunity for SiC in this low-cost design is the SiC diode in the PFC, D5 position in Figure 3. Zero-reverse-recovery current of the SiC diode enables SiC to replace the Si fast diode.
Due to the LLC’s soft-switching topology, a 600 V Si diode will suffice on the output side. In this case, Vf is more important than switching performance.
Device choices for this low-cost design are shown in Table 1.
Power | SiC Diode Voltage Rating | SiC Diode Current Rating |
3.3 kW | 650 V | 10 A or 16 A |
6.6-7.4 kW | 650 V | 20 A or 30 A |
Medium-power high-efficiency OBC architectures (3.3–7.4 kW)
The diode bridge in the conventional PFC wastes power, so the high-efficiency architecture replaces it with a totem-pole PFC. A totem-pole PFC improves efficiency by reducing the number of semiconductor devices in the conduction path from three to two. The totem-pole PFC has been the subject of much theoretical research, but Si MOSFETs limited its use to critical-conduction–mode (CRM) operation and low-power applications due to the commutation of the Si MOSFET body diode. SiC MOSFETs allow operation in continuous-conduction mode (CCM) for high efficiency, low EMI, and high power density. Totem-pole PFC is commonly accepted in high-efficiency design now, as shown in Figure 4.
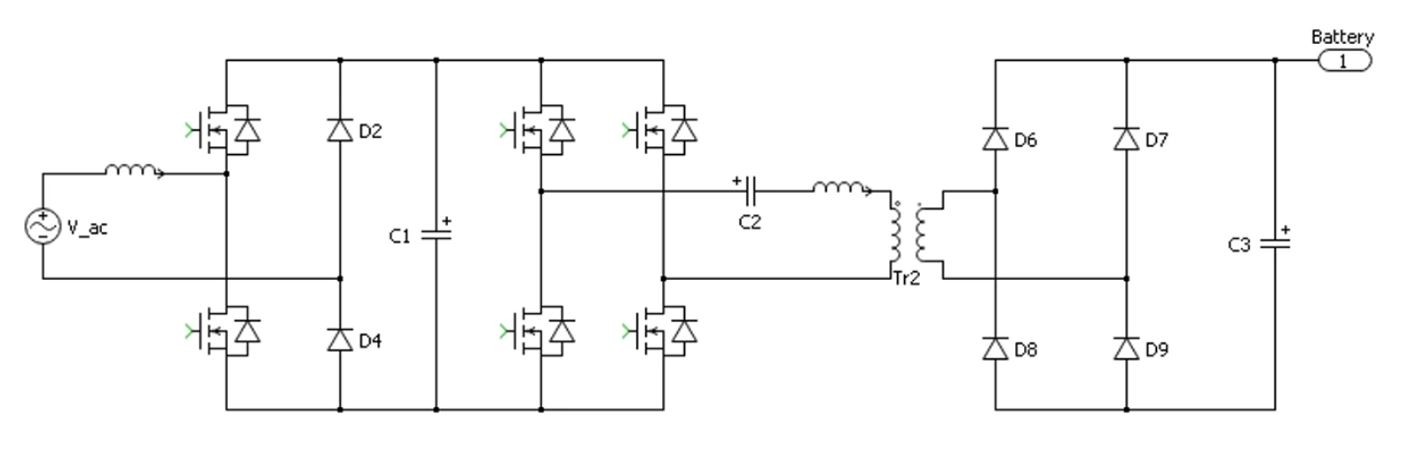
A high-efficiency medium-power design (Figure 4) can achieve peak AC/DC efficiency of >98.5%. The overall system peak efficiency is about 96%.
For example, for a 3.3 kW design, a 60 mΩ, 650 V SiC MOSFET may be used in the PFC stage. Four such devices may be used on the DC/DC side with Si diodes at the output. For a 6.6 kW design, two pairs of 60 mΩ, 650 V SiC MOSFETs may be used in parallel in the PFC stage, or a single pair of 25 mΩ devices.
Device choices for this high-efficiency design are summarized in Table 2.
Power | SiC MOSFET Voltage Rating | SiC MOSFET PFC | SiC MOSFET DCDC |
3.3 kW | 650 V | 60 mΩ | 60 mΩ |
6.6-7.4 kW | 650 V | 2 x 60 mΩ or 25 mΩ | 60 mΩ or 45 mΩ |
Higher-power OBC designs
At higher power levels such as 11 kW or 22 kW, the battery voltage can be either 400 V or 800 V, but as mentioned earlier, the market is trending toward 800 V, beginning with high-performance vehicles.
The high-power design uses three-phase power; the efficiency is >98% for both the PFC and the DC/DC stage, for an overall efficiency of ~96% to 97%. It is possible to produce an 11-kW OBC for a 400 V bus by combining three single-phase 3.7-kW designs in parallel; the power density will be lower and the cost will be higher than a ground-up approach, but reusing an existing design may reduce the time to market. The best results will be obtained from an optimized three-phase design at 800 V bus, such as the architecture shown in Figure 5. The Vienna rectifier is a popular choice for three-phase power correction due to its high efficiency, CCM operation, three-level switching, and reduced voltage stress on the power devices.
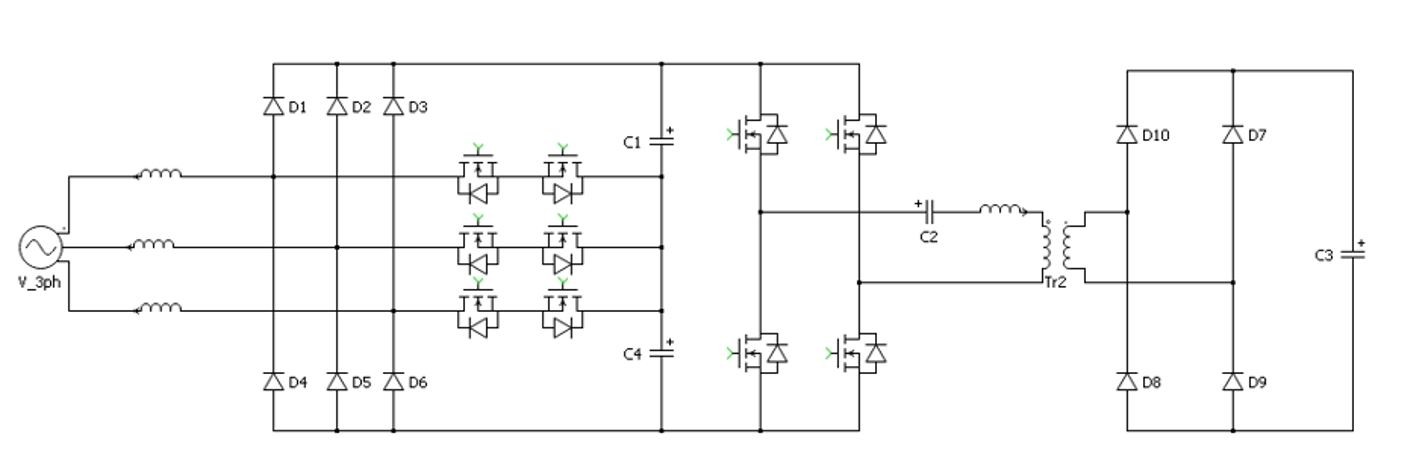
In an all-SiC design, the 11 kW Vienna rectifier uses six E3M0060065K SiC MOSFETs and six E4D20120H diodes. The diodes are 1,200 V devices; the MOSFETs can be 650 V devices, as they see only half of the bus voltage (400 V) due to the three-level switching for the Vienna rectifier.
The full-bridge LLC uses four 1,200 V SiC MOSFETs and four 1,200 V SiC diodes at output. The 800 V bus requires 1,200 V SiC MOSFETs at 75 mΩ or 40 mΩ RDS(on); a 1,200 V Si MOSFET is not competitive in this application and the SiC output diode is preferred to the corresponding Si device due to its lower voltage drop and better switching performance.
For a 22 kW OBC, three 7.4 kW OBCs in parallel can be used, but again, a solution based on the Vienna rectifier with SiC MOSFETs and SiC diodes is the superior approach. The design mirrors that of the 11 kW OBC in Figure 5, but the higher power output requires six lower-RDS(on) MOSFETs (25 mΩ RDS(on)) and six higher-current–rating SiC diodes in the PFC and DCDC.
Device choices for the high-power three-phase design are shown in Table 3.
Power | SiC MOSFET PFC (650 V) | SiC MOSFET DCDC (1,200 V) | SiC Diode PFC (1,200 V) | SiC Diode DCDC (1,200 V) |
11 kW | 60 mΩ | 75 mΩ or 40 mΩ | 15 A or 20 A | 15 A or 20 A |
22 kW | 2 x 60 mΩ or 25 mΩ | 40 mΩ or 32 mΩ | 30 A or 40 A | 30 A or 40 A |
Summary: Silicon Carbide versus Si by application
SiC provides much better performance in terms of efficiency and power density in OBCs than Si devices. When should the OBC designer consider using SiC devices instead of Si? The table below provides a summary.
Power Level | Comments |
Low power (< 2kW) | Low cost is paramount: SiC not competitive |
Medium-power (3.3–7.4 kW) low-cost design | Consider SiC diode in PFC stage |
Medium-power (3.3 kW < 7.4 kW) high-efficiency design | Consider SiC diode and MOSFET in both PFC and DCDC |
High power (11 kW/22 kW) | 1,200-V SiC MOSFET and diode provide higher efficiency, higher power density, and lower system cost than a Si solution. At the output side, for a 400-V battery, a 650-V Si diode provides better efficiency and cost; for an 800-V battery, a 1,200-V SiC diode should be used due to a lower Vf than a Si diode. |
About Wolfspeed Silicon Carbide devices
Wolfspeed SiC MOSFETs address many power design challenges by providing devices with low on-resistance, very low output capacitance, and low source inductance for a perfect blend of low switching losses and low conduction losses. Compared with silicon-based solutions, Wolfspeed SiC power device technology enables increased system power density, higher switching frequencies, reduced component count, and reduced size of components such as inductors, capacitors, filters, and transformers.