What’s Under the Hood? EV Architectures & Inverters
Article
The electric-vehicle market is among the largest and fastest-growing business opportunities for Silicon Carbide (SiC) device manufacturers. Ten million EVs were on the world’s roads in 2020, according to the International Energy Agency (IEA), an organization that urges mass adoption of light-duty EVs this decade to combat climate change.1
As the leading supplier of Silicon Carbide discrete Schottky diodes and MOSFETs as well as power modules, Wolfspeed facilitates success in this market.
This chapter of Wolfspeed’s What’s Under the Hood series introduces various levels of architectures for vehicle powertrain electrification before focusing on two key components in the battery EV (BEV) drivetrain: motors and inverters. We discuss the types and placement of electric motors as well as Silicon Carbide-based inverters and their switching schemes.
End of the ICE age?
The internal combustion engine (ICE) market is in decline, according to industry observers. No major announcements on new ICE R&D investments or addition to roadmaps have been made recently by auto OEMs. This knowledge, combined with an estimate of 41 million EVs and hybrid EVs (HEVs) expected on the road by 2026,2 points to the end of the ICE age.
OEMs have been transitioning to the electric powertrain for years, with the 1997 Toyota Prius introduced in Japan as the first HEV and the 2008 BYD in China as the first plug-in HEV (PHEV). The road to BEVs is thus paved with various levels of “hybridization” that depend on the power of the motor drive:
- Micro and mild hybrids: These “eAssist” systems have belt/integrated starter generators with 12-V “micro” and 48-V “mild” systems with <5-kW and 5- to 13-kW motors, respectively, that deliver the torque required to move the vehicle from a standstill. This architecture is often used by large trucks and SUVs.
- Full hybrids: With 20- to 40-kW motors, HEVs charge purely from their ICE blocks and regenerative braking. The motor and the ICE work simultaneously most of the time.
- Plug-in hybrids: The 50- to 90-kW motors in PHEVs allow electric-only local commutes, with a typical range of 10–50 miles (16–80 km) on a single charge from AC wall power.
Hybrid architectures
Hybrid drivetrains have architectures similar to BEVs, except they have additional energy sources and smaller onboard electric energy storage. A common feature in all hybrid architectures, where Wolfspeed’s SiC modules shine, is the bidirectional inverter that allows the ICE and regenerative braking to charge the battery. There are, however, four major drivetrain arrangements (Figure 1), including series, parallel, fuel-cell, and series-parallel.
The series hybrid, such as the Nissan ePower, Chevy Volt, BMW i3, and some models of the Toyota Prius, comprises an ICE that is in line with the battery and electric motor. The vehicle wheels and the ICE are thus mechanically “decoupled.” A significant portion of the design is that of a BEV with the motor driving the wheels directly. When the on-board battery is depleted, the ICE drives a generator that both charges the battery and powers the electric motor. Whenever a large amount of power is required, the motor draws electricity from both the battery and the generator.
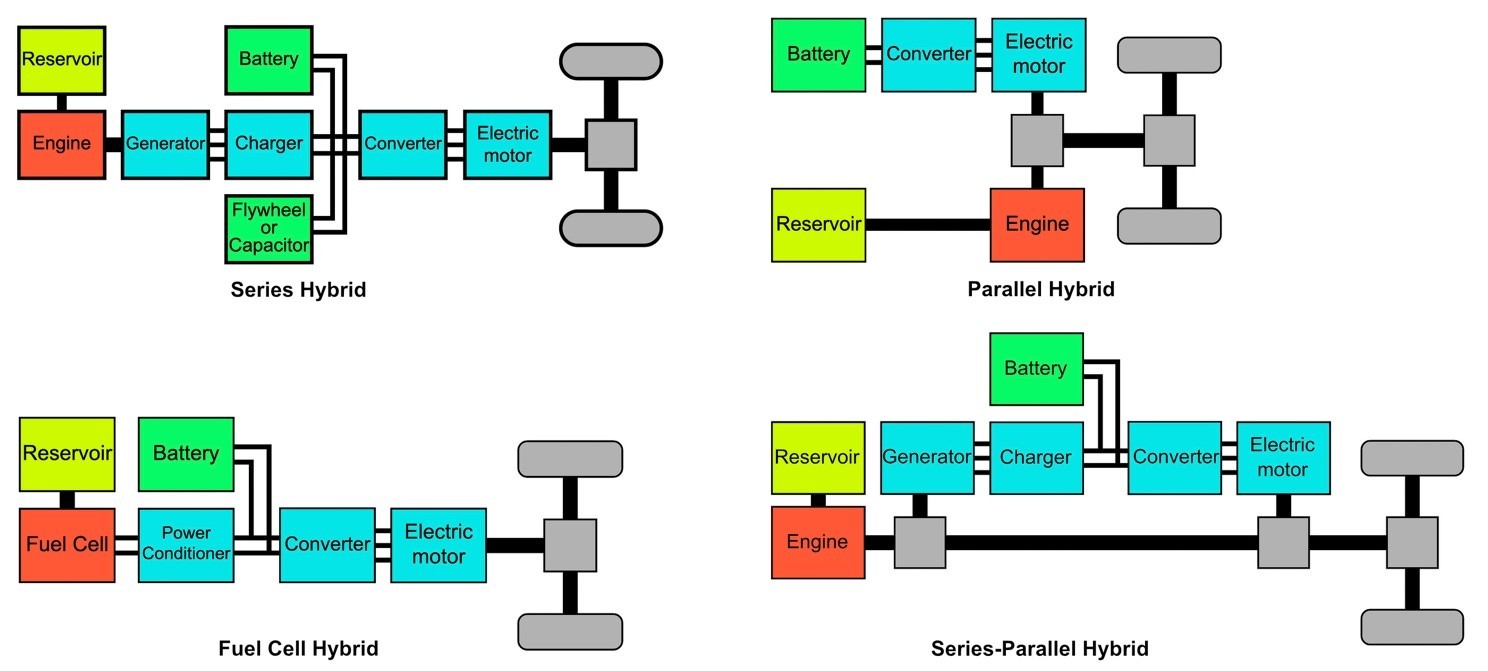
On the one hand, the two energy conversions — mechanical to electrical to mechanical — result in higher losses,3 and on the other, the ICE size and speed can both be optimized for high efficiency. Both the battery pack and the motor in this architecture tend to be larger than in the parallel architecture, making it the more expensive hybrid.
The fuel-cell HEV (FCHEV) uses a design similar to that of the series hybrid, except the ICE and generator are replaced by the fuel cell and a power conditioner that helps the fuel cell output the appropriate voltage and current for the application, in this case charge the battery or drive power to the inverter.
The parallel hybrid architecture, as that found in the Ford Fusion, Honda Civic, and some models of the Toyota Prius, consists of the ICE in parallel to the electric drivetrain. The vehicle is propelled by both the ICE and the electric motor connected to a mechanical transmission that usually comprises a planetary gear system. The power distribution between the ICE and the motor is changed such that they both run in their optimum operating region as much as possible. When the electric motor does not supply rotational power, for instance, the ICE takes over.
Because both the electric motor and, therefore, the inverter are smaller than those in the series architecture, parallel hybrids have lower costs.
The power-split, or series-parallel, hybrid is a combination of both series and parallel architectures, with the intention of utilizing the benefits of both. Planetary gear systems are used to drive the shaft using both the ICE and the electric motor, and a generator to charge the battery is connected to the shaft as well.
All hybrid architectures, except FCHEVs, have been seen by many automakers as a transition to the simpler BEV drivetrain (Figure 2), with the battery, motor, and inverter being the main components involved in traction.
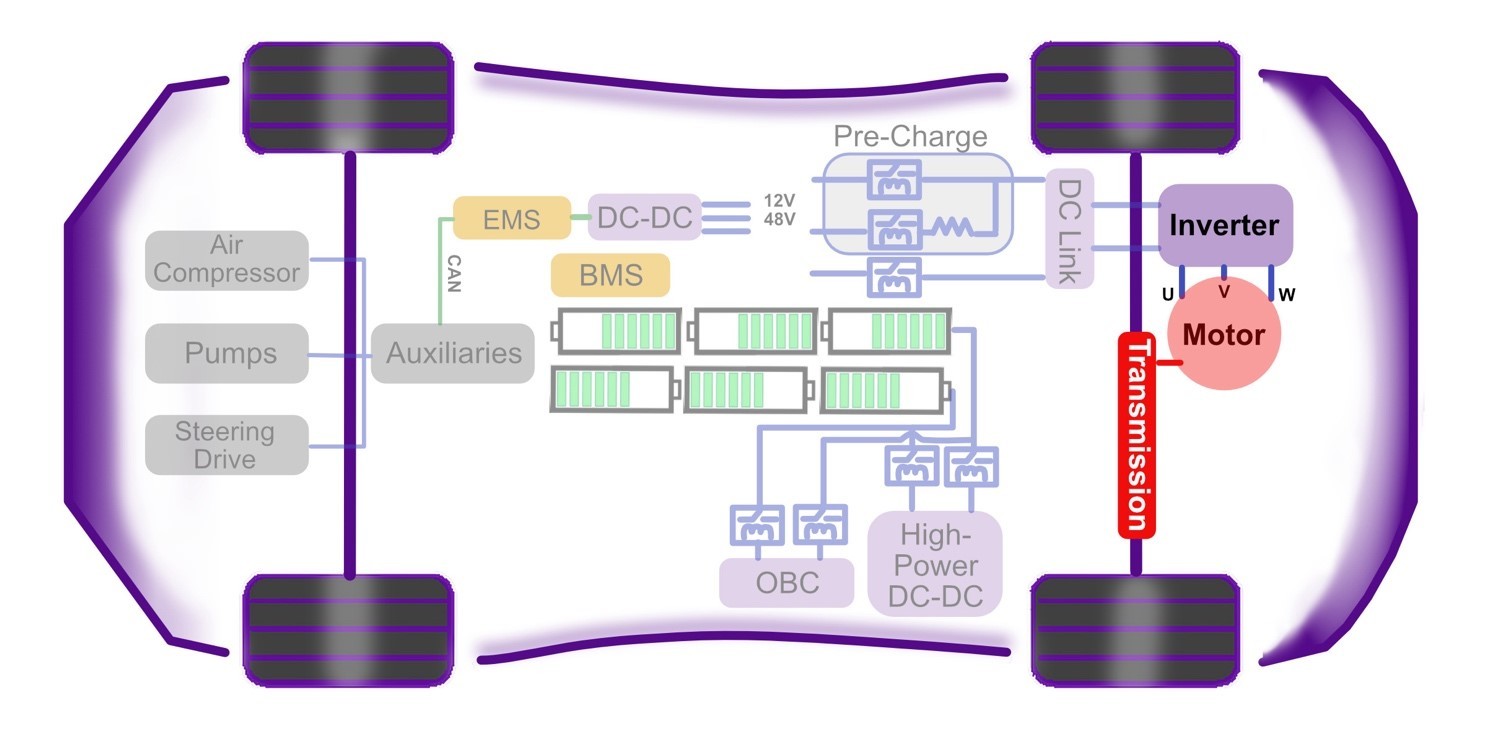
BEV hub motors & e-axles
BEV motors can be classified as hub motors and e-axles based on their mechanical coupling to the drivetrain. Hub motors are mounted at the wheel to drive it directly. The resulting removal of the axle and mechanical gears offers benefits of higher efficiency, smaller motors and inverters, and lower interior floors.
However, hub motors require special control to tune the speed of each wheel to changing requirements, such as when turning the EV needs outer wheels to rotate faster than the inner wheels. Because a differential pumpkin is not available in axle-less designs, the rotational speed differential must be handled by electronic motor control. With an inverter driving and controlling each motor, this design can get expensive. Another challenge is environmental protection from dust, debris, and water, which may require integrating and sealing off all electronics with the motor.
Suppliers of hub motors are fewer, including Protean, Elaphe, and Nidec, compared with those offering e-axles.
Mounting the motor in the center of the axle results in the e-axle design. While this usually requires only one motor per axle, there can be variations. Tesla’s Tri-Motor, for instance, uses two motors on one of the axles.
Although the e-axle usually requires motors to be larger because they drive the full axle, it is cheaper and therefore more popular. It has fewer electronic components because some of the speed control requirements are replaced by cheaper mechanical parts.
Motor types for EVs
BEVs do not use DC motors because of insufficient torque at high speed and rapid wearing out of commutators. Single-phase AC motors are also avoided because they do not deliver sufficient starting torque and have much lower power ratings, making them suitable for the lighter loads of home appliances. Three-phase AC motors, on the hand, offer BEVs high torque from middle to high speeds that can be further tuned to the needs of the drivetrain. BEVs use one of three types of three-phase AC motors — induction, permanent magnet synchronous, and permanent magnet synchronous reluctance.
The induction or non-synchronous motor has no brushes, which avoids wearing out of parts. Rotor windings generate the magnetic fields required — there are no expensive permanent magnets. The motor is directly controlled by the inverter AC output fundamental frequency with a small slip frequency. However, these motors have a low starting torque and are generally found in older BEV model architectures, such as the Tesla Model S.
The permanent magnet synchronous machine is the most common in BEVs, like the Toyota Prius, BMW i3, Audi e-Tron, and Nissan Leaf. Although they are easier to start than an induction motor, they require permanent magnets inside the rotor. With that extra cost also comes higher efficiency because the rotor does not draw current.
The permanent magnet synchronous reluctance machine is a newer motor that is more efficient than pure induction motors. They have a higher power density, but they are more complex to control. They are used, such as in the Tesla Model 3, for their lower inertia that helps achieve higher acceleration.
Traction inverters
The traction inverter converts the high-voltage DC from the battery to the three-phase AC needed by the motor (Figure 3). However, not all designs use the boost converter shown in the figure.
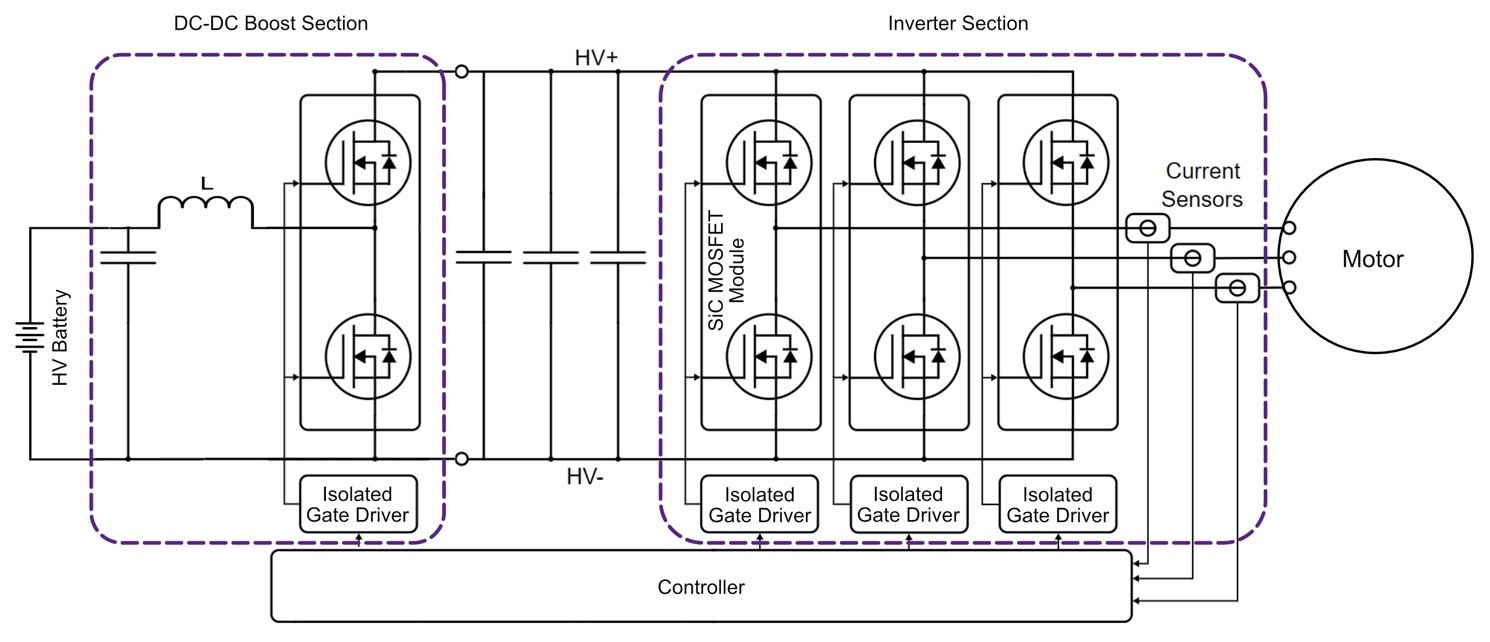
Bidirectional inverters needed for regenerative braking are best implemented with SiC power modules because they allow for higher efficiency, greater power density, and simpler circuits compared with silicon IGBT components.
The inverter is usually required to output square waves with switching frequencies between 6 kHz and 24 kHz. This output is filtered by the motor’s inherent inductance to provide a fundamental electrical frequency, which is also the shaft rotational speed for synchronous motors.
Although the classic pulse-width–modulation (PWM) scheme is used by most modern microcontrollers and is easy to implement for motor control, it is not common in traction inverters because it is not the most efficient switching scheme. Instead, the space-vector PWM (SV-PWM) is used in BEV applications. It allows overmodulation for attenuating the top of the sine waves so that a voltage higher than the DC-link bus voltage can be applied and greater current driven through the motor (Figure 4). This scheme also minimizes the switching transitions in the six switches of the inverter, thereby lowering switching losses and increasing efficiency.
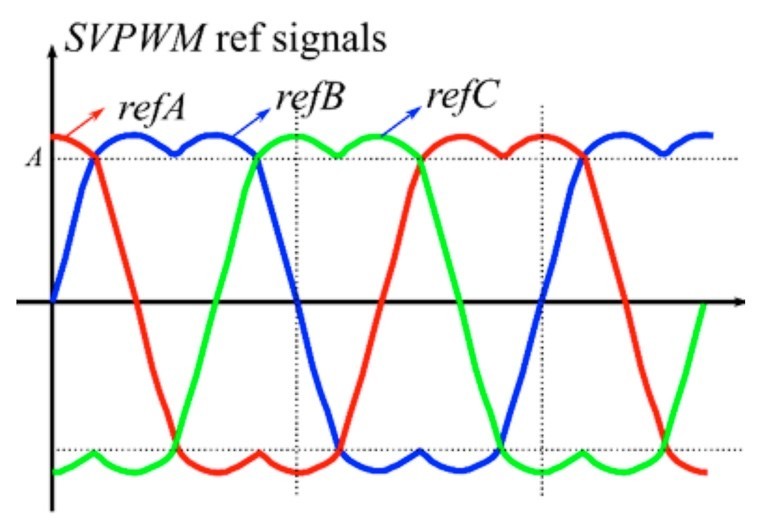
BEVs eschew the open-loop variable-frequency control in favor of the closed-loop field-oriented control (FOC) because the former uses a lookup table instead of feedback to get only low-precision speed control. The FOC adds expense with rotor-angle position encoder and phase-current–sensing requirements but can set up the electric fields necessary in various operating modes — hill-hold, maximum acceleration, high speed, braking, and even faults.
An active short-circuit (ASC) feature is also used with inverters to handle faults, such as preventing very high power being delivered to the battery when regenerative braking is engaged at high speed. The ASC shorts the motor phases for the several milliseconds needed by contractors to open the circuit and protect the battery.
Conclusion
For less than $1, a BEV travels the same distance that an ICE-based vehicle travels on a gallon of gas, according to the U.S. Department of Energy. Wolfspeed’s SiC enables all critical and many auxiliary functions in BEVs.
To gain further knowledge of this important application and the functional blocks that Wolfspeed products enable, visit the Power Products Knowledge Center.
References
- IEA. “Global EV Outlook 2021.” https://iea.blob.core.windows.net/assets/ed5f4484-f556-4110-8c5c-4ede8bcba637/GlobalEVOutlook2021.pdf
- Yole Développement. “Electric Vehicles: Silicon Carbide (SiC) era has just begun.” https://www.yolegroup.com/
- Benevieri, et al. “Series Architecture on Hybrid Electric Vehicles: A Review.” https://www.mdpi.com/1996-1073/14/22/7672/pdf