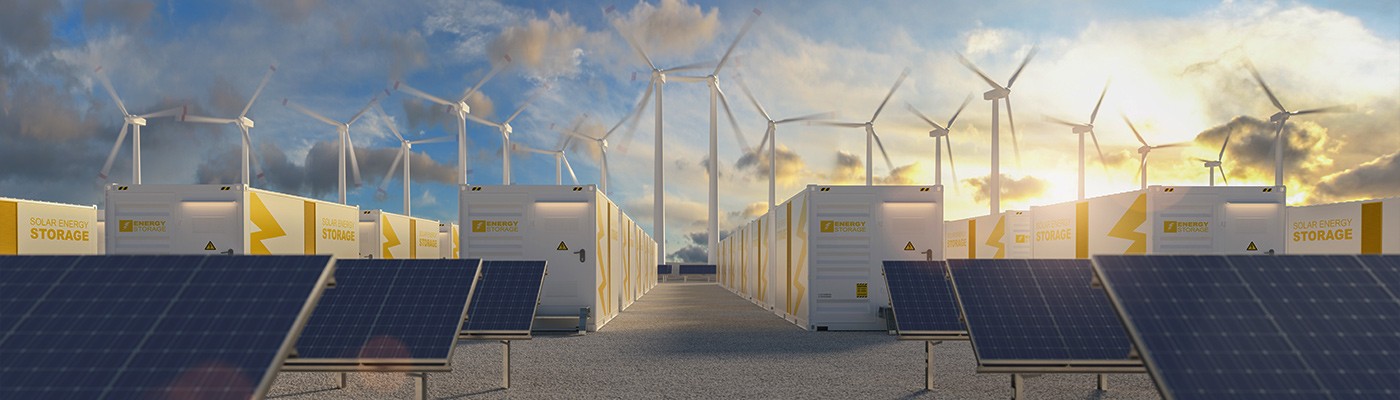
Energy Storage Systems
Wolfspeed Silicon Carbide is capable of incredible reliability and efficiency within battery-based energy storage systems, meaning power is always available even when the sun sets.
Energy Storage Systems Enable a Secure Energy Future
One of the biggest challenges facing the renewable industry is how to manage supply vs demand, as power generated by solar and wind systems can fluctuate considerably depending on environmental conditions and time of day. Battery-based Energy Storage Systems (ESS) are one way that system designers can address this challenge and create a reliable energy infrastructure at the residential, commercial, industrial and utility levels.
Wolfspeed Silicon Carbide MOSFETs, Schottky diodes and power modules are the gold-standard for energy storage systems, creating systems that are more efficient and power dense, have simpler circuit topologies that reduce overall cost and size, all while meeting emerging efficiency standards.
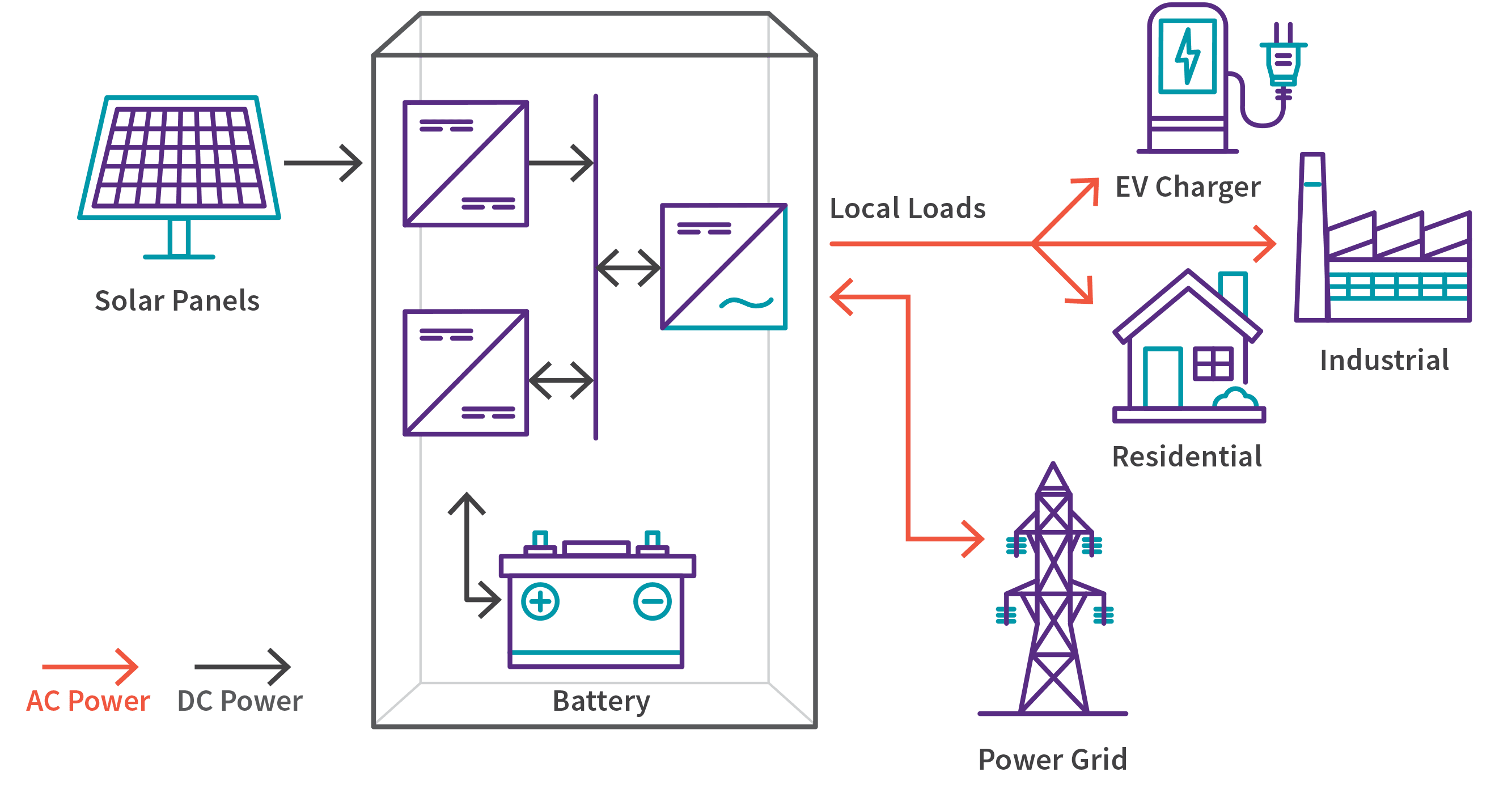
Residential and Commercial Energy Storage Solutions
Solar photovoltaic and wind energy storage systems have multiple power stages that can benefit from Wolfspeed Silicon Carbide MOSFETs, Schottky diodes and power modules, including the Wolfspeed WolfPACK™ family of devices. Whether it is a single-phase residential system (5-15 kW) ore three-phase commercial system (30-100 kW), the architecture and power circuit topologies are similar and can be scaled according to power level.
At the residential and commercial level, energy storage systems save excess power generated during peak times for the building it is tied to. Using Wolfspeed Silicon Carbide in a residential or light commercial buck/boost battery interface circuit can improve charge and discharge efficiency while reducing system cost and size.
Utility-Scale Energy Storage Solutions
Larger industrial and utility-scale energy storage systems utilize massive battery storage systems that operate before the meter, storing enough power for large factories or entire utility grids. These large-scale ESS can also benefit from Wolfspeed Silicon Carbide in the buck/boost circuit. Currently, using Wolfspeed’s 1200 V MOSFETs and Schottky diodes in a three-level configuration or WolfPACK™ Six-Pack Modules provides an ideal combination of efficiency and ease of design along with the highest system power density. New 1500 V photovoltaic solar systems are delivering higher voltage to energy storage systems.
Accelerate your solar system design process with SpeedFit™ Design Simulator
Watch as Wolfspeed's Zan Huang demonstrates using the SpeedFit™ Design Simulator to simulate a solar MPPT Boost Converter and see how you can achieve high efficiency and power density in solar systems even under elevated temperatures.
When You Need Power You Can Rely on, Choose Wolfspeed
Alternative energy systems are an alternative only when they can be counted on, which is why Wolfspeed is a great choice. Wolfspeed SiC’s robust performance has proven its value time and again, with billions of field hours for our most popular SiC components.